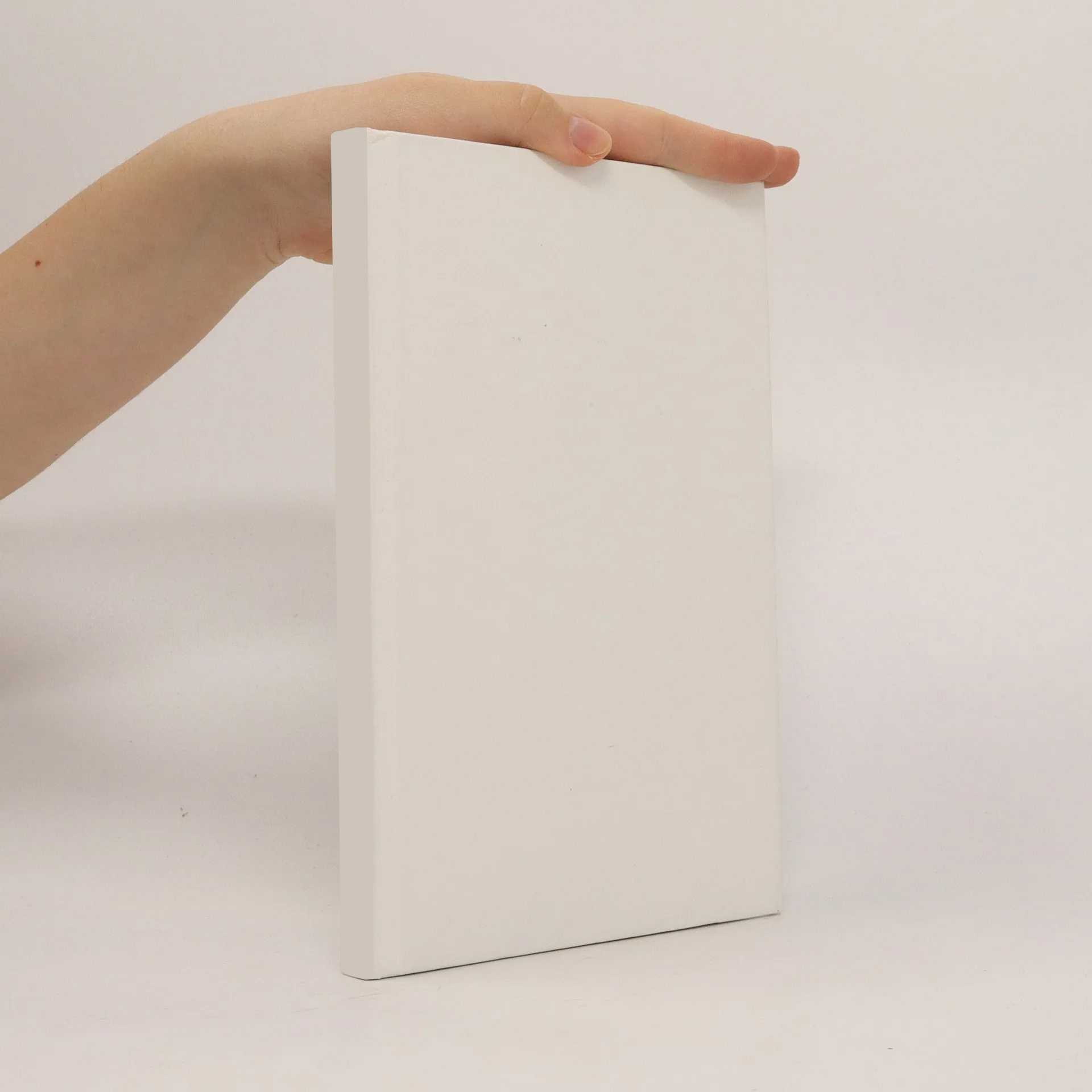
Beschreibung des Kristallisationsprozesses mittels eines neuen mikroskaligen Modells für teilkristalline Thermoplasten
Autoren
Mehr zum Buch
In many industrial sectors, plastics are among the most important materials these days, because the large variety of diff erent polymers enables a target-oriented selection of materials for almost every application. The material-specific properties can be used specifi cally to meet the component requirements. In times of rising demands on the part properties and complexity, it is therefore of great importance to know the fi nal material properties as early and accurately as possible using new simulation approaches. For semi-crystalline materials, this requires new multiscale approaches, which take into account the crystalline superstructures. The aim of the presented work is the defi nition, implementation and validation of a new crystallization model for the time-resolved calculation of the solidification process in semi-crystalline thermoplastic melts at the microscale. Thereby, the boundary conditions, which are put on the melt during the manufacturing process, are taken into account. Following the concept of nucleation and growth, a nucleation model is derived from the formalism of Ziabicki. In contrast to Ziabicki’s work the Gibbs free energy is kept as model parameter as long as possible, because it can be used to introduce the infl uence of the manufacturing process in the model description. To map the non-linear viscoelastic behaviour of plastic melts, relaxation functions based on the reptation theory are used. The event-based realization of the model is presented together with the required numerical methods. A verifi cation of the crystallization model takes place in the context of application examples for the injection moulding process. For this, the software package is used in multiscale simulation chains, in which a macroscale simulation of the manufacturing process provides the boundary conditions for the microstructure simulation. The calculated spherulite distributions are in good agreement with polarized light microscopy fi gures of parts manufactured with the same process conditions. To show the potential of the microstructure simulation, the infl uences of the process parameters on the spherulite diameter are examined automatically with a design of experiments for the simulation runs. Moreover, eff ective material properties are derived from the calculated microstructures using a new asymptotic homogenisation scheme. Here, the eff ective Youngs’ moduli and the thermal conductivities are predicted over the wall thickness of an injection moulded part. The results are in good agreement with the experimentally expected value ranges and demonstrate the influence of the manufacturing process on the inhomogeneous material properties.