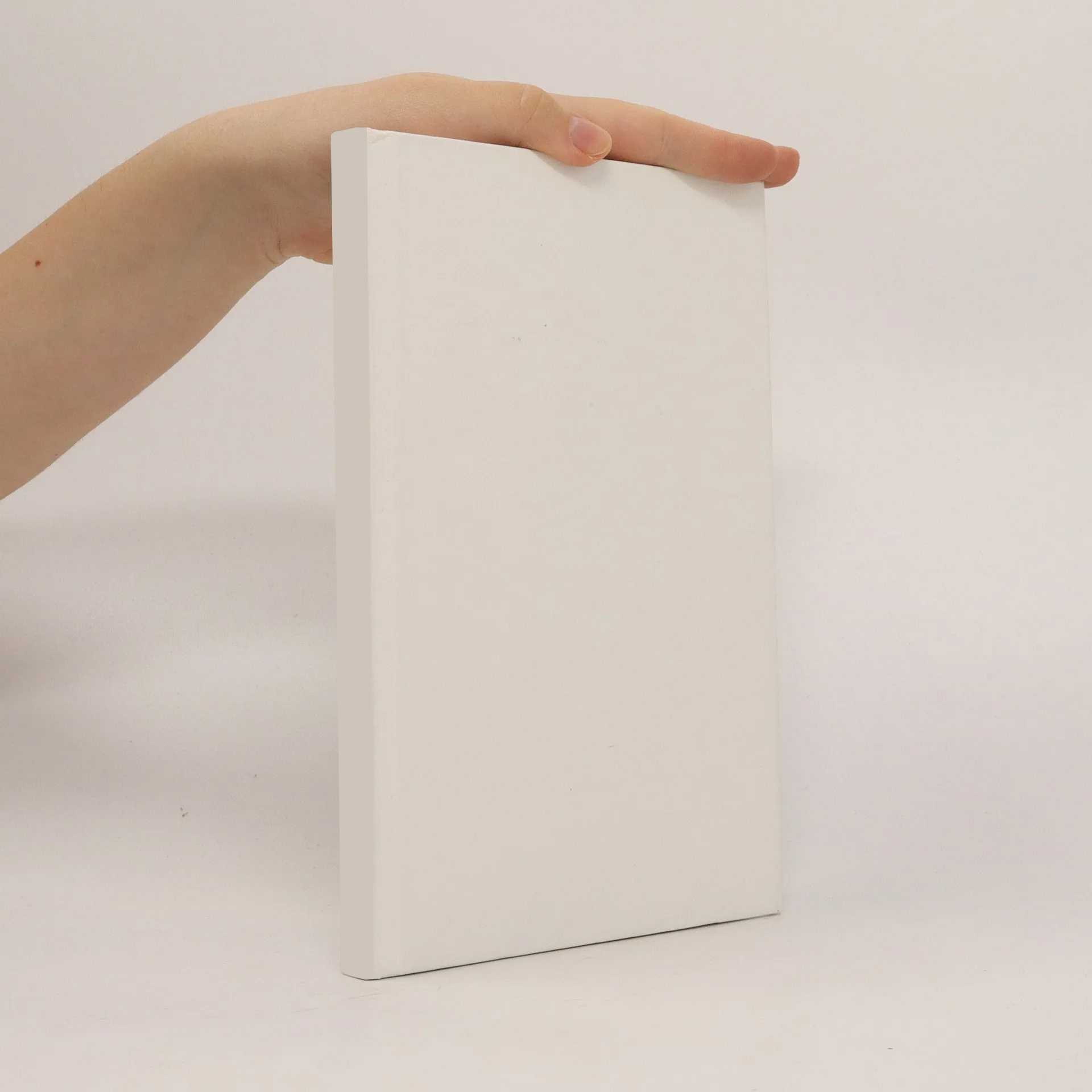
Modular permanent-magnet synchronous motors with high electromagnetic utilization
Autoren
Mehr zum Buch
Variable speed electric drive systems became very important in recent years in many ranges of mechanical engineering as replacement for mechanical drive components, based on their technical advantages and cost reduction possibilities, due to the continuous developments in this area. Industrial customers are looking for compact drive systems with small volume, which offer higher efficiency and a reduced heat generation. Therefore, a big demand exists for electrical drives with high power- and torque density, which produces at the same time small losses. Basically, all types of electrical motors can be used in drive systems, but not many of them could fulfill all of these demands. The most widely used drive motors are asynchronous induction motors, permanent magnet (PM) synchronous motors and switched reluctance motors. The best solution for general purpose seems to be the permanent magnet synchronous motor, due to its high efficiency and good dynamic and variable speed properties. It also presents the highest development potential at the moment, as its power- and torque density can be increased with the use of high energy rare earth permanent magnets, combined with flux concentration and reluctance torque. The efficiency can be further improved by using the tooth-wound coil technology, which reduces the losses in the stator windings. The aim of this thesis was to develop two permanent magnet excited synchronous motors with 45 kW rated power and speeds up to 3000 rpm, as an alternative to squirrel cage asynchronous motors, used nowadays in the middle power range. Different motor topologies are considered, in order to find the best solution for the given requirements. This thesis deals with the design optimization of two high-torque density permanent magnet motors with different kinds of water jacket cooled stator and PM rotor using the tooth-wound coil technology, being fed by inverter, for typical industrial applications as variable speed drives. Details of the design and manufacturing process of the motors, the testing conditions and applied computation methodology are presented. The two prototype motors have fractional slot numbers per pole and phase 1/2 (two layer winding) and 1/4 (single layer winding with intertooth), and were designed for continuous rated power of 45 kW between the rated speed of 1000 rpm and a maximum speed of 3000 rpm, but the measurements proved that the field weakening can be extended up to 5000 rpm. Segmented magnets were used for the rotors in order to reduce the rotor eddy current losses due to the concentrated stator winding, which determines a high harmonics content of the air gap field. As comparison, a rotor with nonsegmented magnets was also considered and measured in combination with the original stators, but proved to generate too high losses in the magnets, which heat up the magnets above their thermal limit. The water jacket cooling of the stator gives at rated operation a thermal reserve of 30 K at 1000 rpm to the Thermal Class F limit temperature for the basic motors. Thus it was possible to increase the power for the rated speed up to 53 kW, which corresponds to 34.8 kNm/m3 per active motor volume, including winding overhangs.