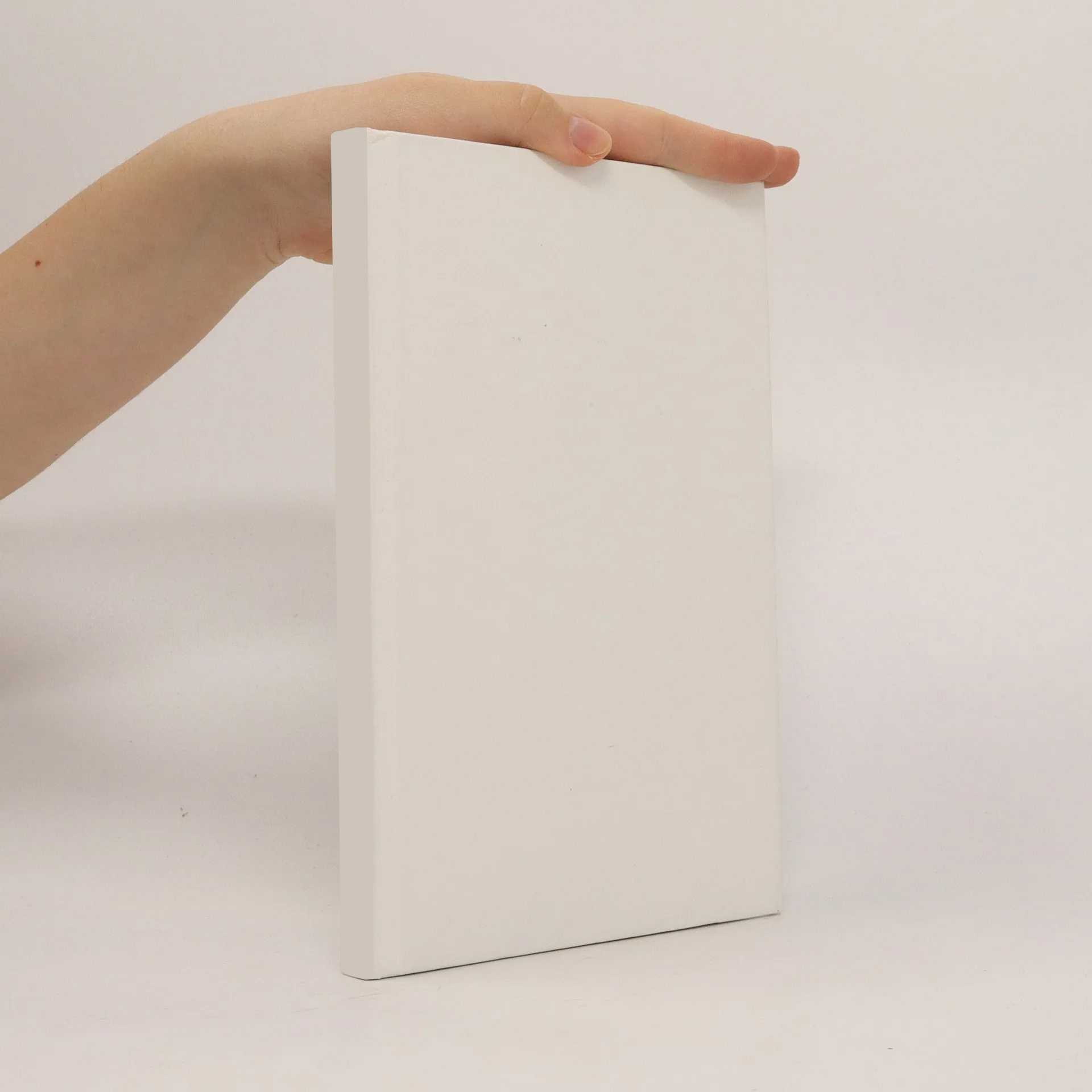
Mehr zum Buch
The present work covers the phenomenological process simulation and the multiscale tool simulation directed to a hybrid forming process. Thereby, the focus is specifically directed onto the forming tool, which is subjected to cyclic thermo-mechanical loading conditions during tool life. In the first part of this thesis an experimental and simulative methodology is introduced and applied for the determination of reference values for tool lifetime. Thereby, essential steps are the choice and application of an appropriate material model for the forming tool, the identification of material parameters using stress/strain experiments and least-squares functionals, the numerical simulation of the hybrid forming process, the experimental validation of the simulation and the performance of fatigue tests with thermomechanical boundary conditions obtained from the numerical simulation. The developed methodology is capable to quantify the thermo-mechanical loading of the forming tool during the hybrid forming process. Further, it delivers reference values for tool lifetime based on the numerical results. Regarding the multiscale tool simulation in the second part of this thesis coated forming tools are considered. Here, essential steps are the development of a theory for a two scale model considering multi-layered coatings, the application of the theory in the context of finite element modelling and the performance of simulation examples considering coated forming tools. The developed theory is successfully implemented on the material level and simulation examples show the applicability of the two scale methodology for the simulation of coated forming tools.
Buchkauf
Phenomenological process simulation and multiscale tool simulation directed to a hybrid forming process, Kim Henning Sauerland
- Sprache
- Erscheinungsdatum
- 2013
Lieferung
Zahlungsmethoden
Keiner hat bisher bewertet.