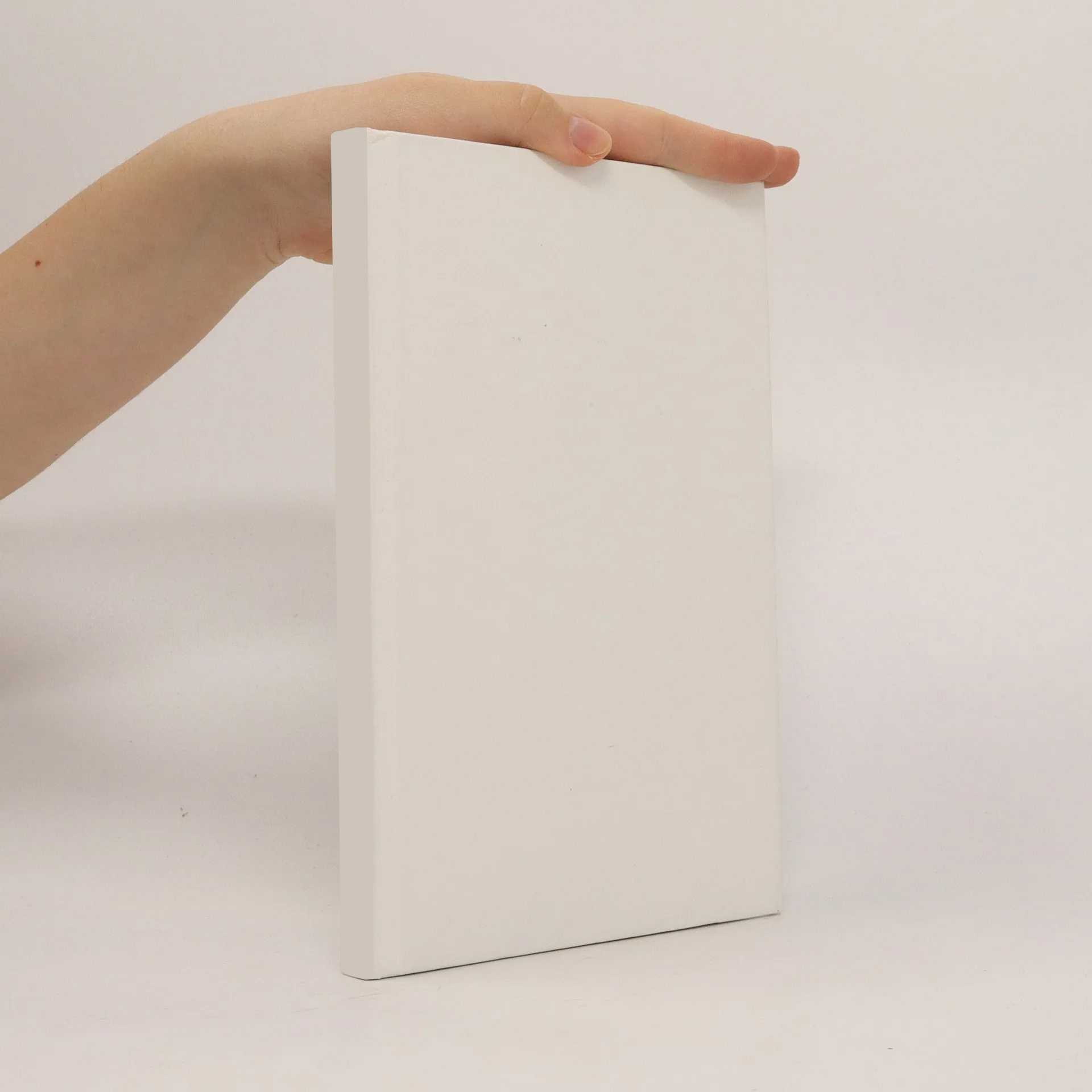
Parameter
Mehr zum Buch
The design of a component and its durability can be improved and assured to a great degree by means of a specific setting of its residual stress state. This is referred to as stress engineering. Prime examples of this are gear wheels (Townsend 1992, Krug 2005), which are usually case-hardened or nitrided and shot peened, particularly at working surfaces and depth of teeth. As a consequence, compressive residual stress depth distributions are introduced in the surface layer, frequently at geometrically complex regions. Such types of residual stresses play a key role in terms of preventing crack growth and reating a lightweight design. If this surface treatment is not applied, the gear wheels experience damage after a number of load cycles. Similar statements can be made for turbine blades and crankshafts, which exhibit complex geometries as well. These machined components are usually shot peened at the blade roots (Feldmann 2012) or deep rolled at the fillets, respectively (Haibach 1982). In this respect, it is necessary to develop reliable measurement methods which are capable of determining residual stress states qualitatively and quantitatively during manufacturing processes and over the lifetime of components. Residual stresses usually vary in their penetration depth with more or less steep gradients that are frequently multi-axial and change their orientation. Since residual stress states can be very complex, the demands for precise measurement methods are high. This study is a good example of appraisal of RS results with a critical eye, particularly for comparisons between measurement methods that differ from their physical principles and from their specific boundary conditions.
Buchkauf
A contribution to enlarge the application limits of residual stress analyses by the hole-drilling and the ring-core method, Andreas Nau
- Sprache
- Erscheinungsdatum
- 2016
Lieferung
Zahlungsmethoden
Keiner hat bisher bewertet.